EnBW Baltic 2 wind farm
The 80 large wind turbines at EnBW Baltic 2 rise high above the waves of the Baltic Sea. The second EnBW wind farm was officially placed into operation on 21 September 2015. The turbines use the powerful and constantly blowing wind to generate electricity for an aggregate of 340,000 households.
Project details
EnBW Baltic 2: Wind power XXL
Webcam EnBW Baltic 2
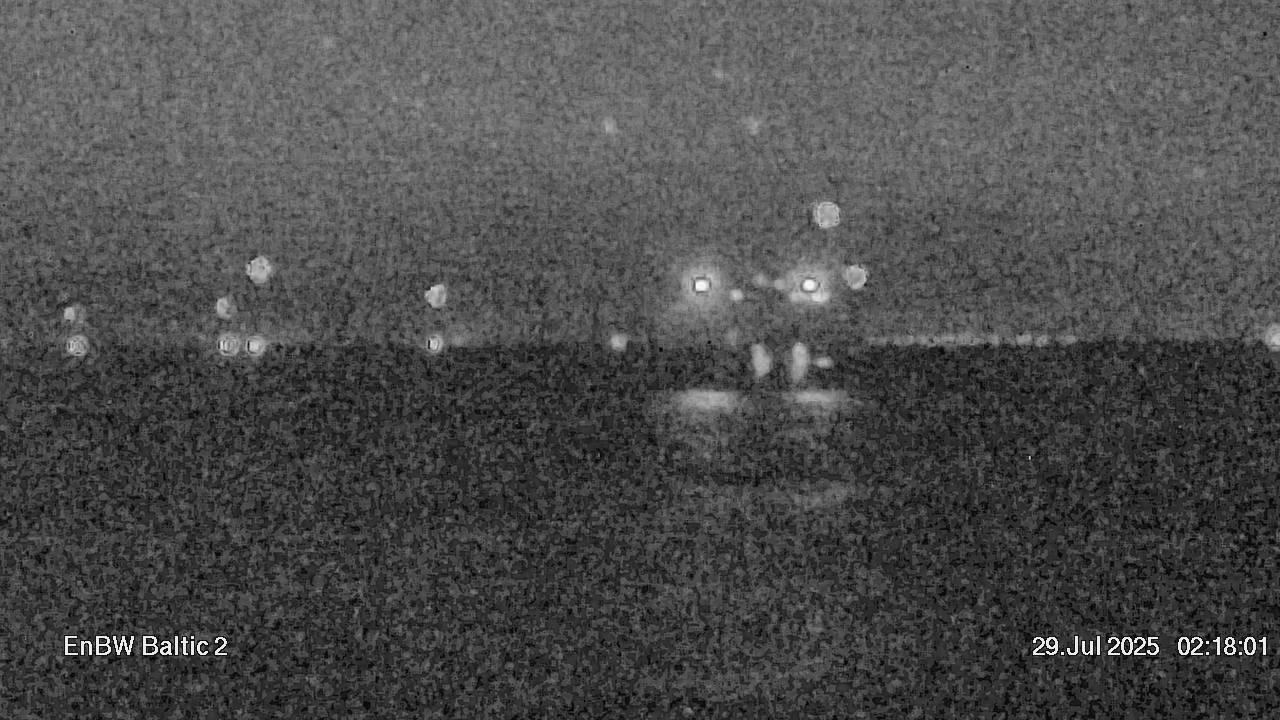
Webcam EnBW Baltic 2
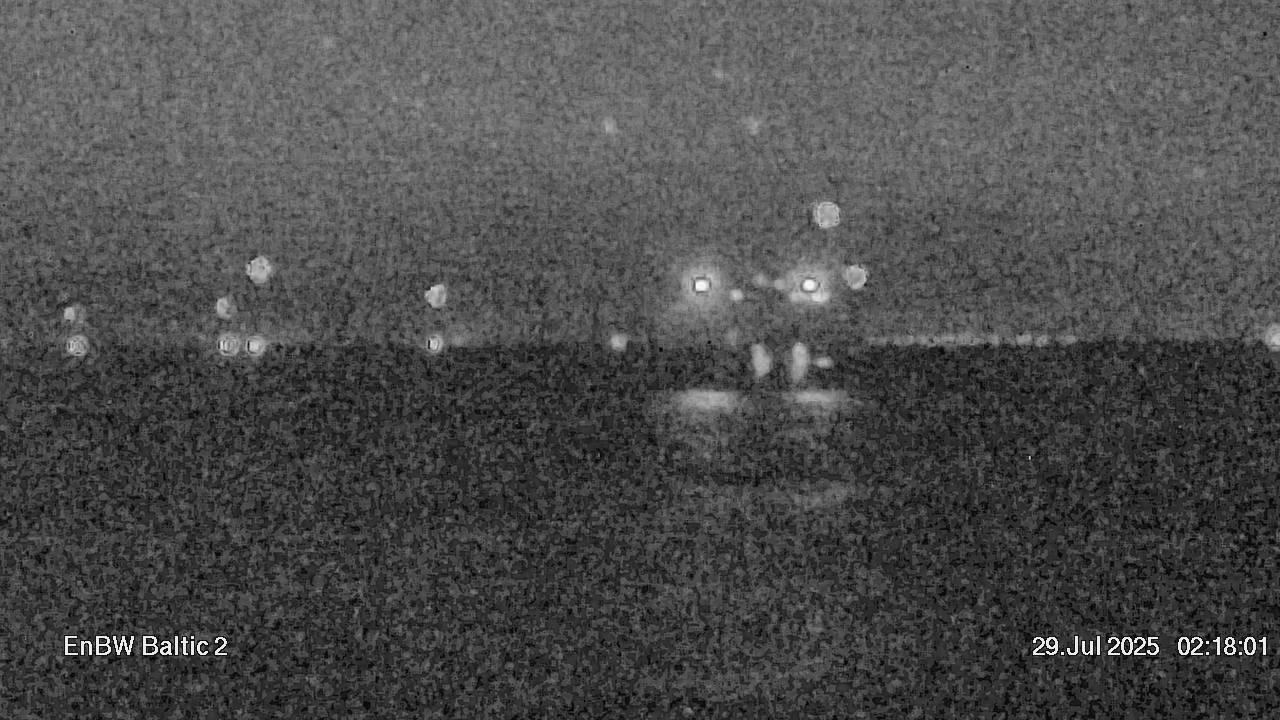
Facts
Location:
|
Baltic Sea, 32 km north of the island of Rügen
|
Size:
|
approx. 27 km²
|
Wind turbines:
|
80 Siemens SWT-3.6-120
|
Foundations:
|
39 monopiles (approx. 23–35 m) and 41 jackets (from approx. 35 m)
|
Water depth:
|
23–44 m
|
Total output
|
288 MW
|
Annual yield
|
1.2 billion kWh
|
Average wind speed
|
approx. 9.7 m/s
|
EnBW Baltic 2 has significantly larger dimensions than our first wind farm in the Baltic Sea – EnBW Baltic 1. The planning and logistical challenges faced in constructing the wind farm were considerably greater. EnBW Baltic 2 has wind turbines that are almost a third larger than those at Baltic 1. On an area covering 27 square kilometres, it is four times larger than EnBW Baltic 1 and can generate six times as much electricity.
The depth of the sea at the wind farm varies between 23 and 44 metres. Depending on the sea depth, the wind power plants were either mounted on steel piles, so-called monopiles (up to around 35 metres), or steel framework structures, so-called jackets (from around 35 metres). An annual yield of around 1.2 billion kilowatt hours means that the EnBW Baltic 2 wind farm can supply an aggregate of around 340,000 households per year and thus save around 900,000 tonnes of CO₂ emissions.
As we did for Baltic 1, our first offshore wind farm, we have also brought an investment partner on board for Baltic 2, with almost half of the shares (49.9%) owned by BSOH. BSOH is a holding company held by the cooperative pension fund PGGM and Ärzteversorgung Westphalen-Lippe. The other 50.1% stake is in the hands of EnBW, along with all operation and maintenance tasks. Our investment models give us additional financial leeway for further growth projects.
Construction diary Baltic 2
The 80th and final wind turbine was installed on its foundations at around 2:30 p.m., marking the successful completion of all turbines in the EnBW Baltic 2 wind farm
EnBW Baltic 2 feeds the first kilowatt-hours of electricity into the grid. At this point, 58 of the 80 wind turbines have been installed. They will gradually be connected to the grid. Once the entire wind farm is in place, it will have a total output of 288 megawatts and be able to generate electricity for around 340,000 households.
After around seven months, the main installation work on the foundations in completed. More than 80,000 metric tons of steel were used in the process. Half of the 80 wind turbines have also been fully installed. It takes around 18 hours on average to build a turbine.
By the end of 2014, work is coming along well at the EnBW Baltic 2 construction site: The OSS substation has been installed, along with 68 foundations. What’s more, 34 wind turbines have been built. A total of 59 stretches of cable have been laid in the wind farms internal cable network.
Premiere: The first wind turbine for EnBW Baltic 2 is built.
Baltic 2 technology
Building 80 wind turbines and a substation and connecting the entire 27 km² area with around 85 km of submarine cables requires precise planning. All individual processes must be precisely coordinated: The cables can only be laid within the wind farm once the foundations have been completed. Then the wind turbines are built. The substation must be completed in good time before the wind farm’s cables are laid and the first turbine built.
Our site managers and logistics specialists can expect challenging tasks, such as estimating the working speeds, calculating the transport routes – and coordinating everything with the weather conditions.
One single ship for the wind turbines, up to two ships for the foundation structures and up to three ships for connecting the cables travel from different ports and arrive at the construction site at different times. The site is further secured by a sea traffic management vessel.
The sea is a capricious project partner: It must not be too cold, otherwise the special cement used to join the foundation components will not set.
The transformer platform needs calm seas to reach its destination and set itself up. The wind turbines can only be installed at wind speeds of up to force 4–5.
For each construction phase, all components not only have to be transported to and installed at the site, which lies 32 km off the German coast, but the crews also need to be regularly replaced.
Even though it only takes around two hours for the crew transfer ships to sail to the construction site from our base port in Sassnitz, a heavy installation platform can take up to 12 hours to get there. As such, it is essential to think of everything – because every delay can cost a six-figure sum each day.
Logistics and coordination
The same white chalk in the famous chalk cliffs of Rügen can be found in the Baltic Sea. On top of this is the so-called boulder clay, a layer of sediment that formed during the melting of the Ice Age glaciers. The foundations are driven between 36 and 55 meters into the ground in order to ensure that they are securely anchored.
Each foundation must be individually adapted to different sea depths ranging from 23 to 44 meters. Monopiles up to 35 meters long are used, depending on the water depth. From a depth of 35 meters, three-legged jackets are used.
The monopiles and the foundation piles for the jackets are driven into the seabed using a pile driver aboard a special ship. The so-called transition pieces, which connect the foundation to the tower, are then placed over the monopiles like a cuff and firmly joined using a special cement.
For the three-legged jackets, the position of the foundation piles is precisely determined by large templates on the seabed.
Only then are the jackets set on the piles and firmly joined using a special cement. It can take up to five days to install a foundation, depending on weather conditions.
The foundations
The components are manufactured at various locations in Denmark and delivered to Mukran Port in Sassnitz, where we are based. Here, the steel towers, nacelles and rotor blades are stored on an area covering 80,000 square meters and pre-assembled two to three months before installation begins.
Components for several turbines can be towed to the construction site on a floating assembly platform. In order to lift the enormous weights, the platform stands on legs firmly secured on the seabed and rises about 10–15 meters above the water level. Each turbine is installed from this platform in around 36 hours.
The steel towers, which weigh 256 metric tons and are around 66 meters tall, are placed on the foundations using a crane and bolted together. The nacelle, which weighs around 150 metric tons, is mounted with the generator and the gears. Finally, the individual rotor blades are installed.
.
Wind turbines and construction
Measuring 40 x 40 meters wide and 14 meters high and weighing 4,400 tons, the transformer platform floats on its own. Besides saving transport costs, the installation of the platform is also less complex: It brings the upper section of its foundations with it in an inwardly retracted state and can therefore base itself on the preinstalled lower section.
Firstly, tugboats tow the transformer platform from the shipyard to the construction site. Once in position, it lowers its jacket foundation structure and lifts itself up about one meter above sea level. Only the substructure on which the jacket structure sits must firstly be anchored to the seabed using foundation piles.
The electricity from the 80 wind turbines flows into the substation and is transformed from a voltage of 33 kV to 150 kV. A low voltage requires a very thick cable to transport electricity in order to prevent transmission losses.
To avoid having to lay such a cable underwater for several kilometers, the electricity is transformed as close as possible to the generation source, which is why the transformer platform is installed at the wind farm on the high seas rather than on land.
Transformer platform and installation
The wind farm’s internal power grid is around 85 kilometers long. The cables are transported to the construction site directly from Norway.
Besides transporting the electricity, the 11.9- and 14-centimeter-thick submarine cables also transmit information and data between the turbines and the control room in Barhöft via highly sensitive optical fibers that are integrated into the cables.
The so-called export cable transports the electricity from the substation via EnBW Baltic 1 to the nearest substation on land. Here, at Bentwisch substation, the voltage is once again transformed from 150 kV to 380 kV and fed into the German grid by 50Hertz Transmission GmbH.
Wind farm cabling and grid connection
Many leading international companies from the wind power and offshore industry, along with regional specialists, are involved in the planning, logistics and construction of our wind farm.
Foundations
(Design, manufacture, transportation and installation): |
HGN joint venture (Hochtief Solutions, GeoSea, Nordsee Naßbagger) Hamburg, Germany
|
Internal wind farm cabling
|
Transportation and laying: Siem Offshore Contractors GmbH, Leer, Germany
Cable manufacture: DRAKA, Drammen, Norway |
Transformer platform
(Design, manufacture, transportation and installation): |
Alstom Weserwind joint venture, Bremen, Germany
|
Wind power plants
(Design, manufacture, transportation and installation): |
Manufacture: Siemens Windpower, Brande, Denmark
Transportation and construction: HGN joint venture (Hochtief Construction, GeoSea, Nordsee Naßbagger), Hamburg, Germany |
Provision of the necessary port infrastructure
|
Mukran Port, Sassnitz
|
Delivery of cable protection systems:
|
Tekmar Energy Ltd., Newton Aycliffe, UK
|