Windpark in der Ostsee: EnBW Baltic 2
Hoch über den Wellen der Ostsee erheben sich die 80 großen Windkraftanlagen von EnBW Baltic 2. Am 21. September 2015 ging der zweite Windpark der EnBW offiziell in Betrieb. Aus dem starken und stetig wehenden Wind erzeugen die Windräder Strom für rechnerisch 340.000 Haushalte.
Projektdetails
Lageplan EnBW Baltic 2
Webcam EnBW Baltic 2
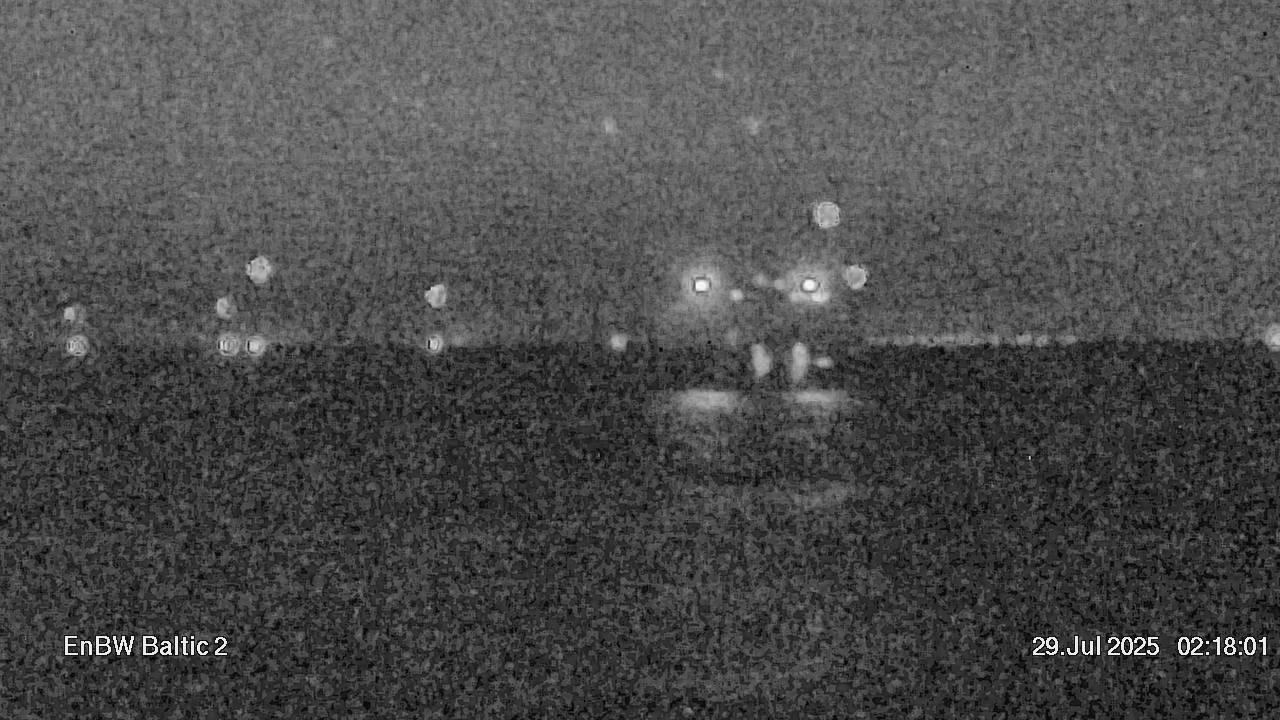
Webcam EnBW Baltic 2
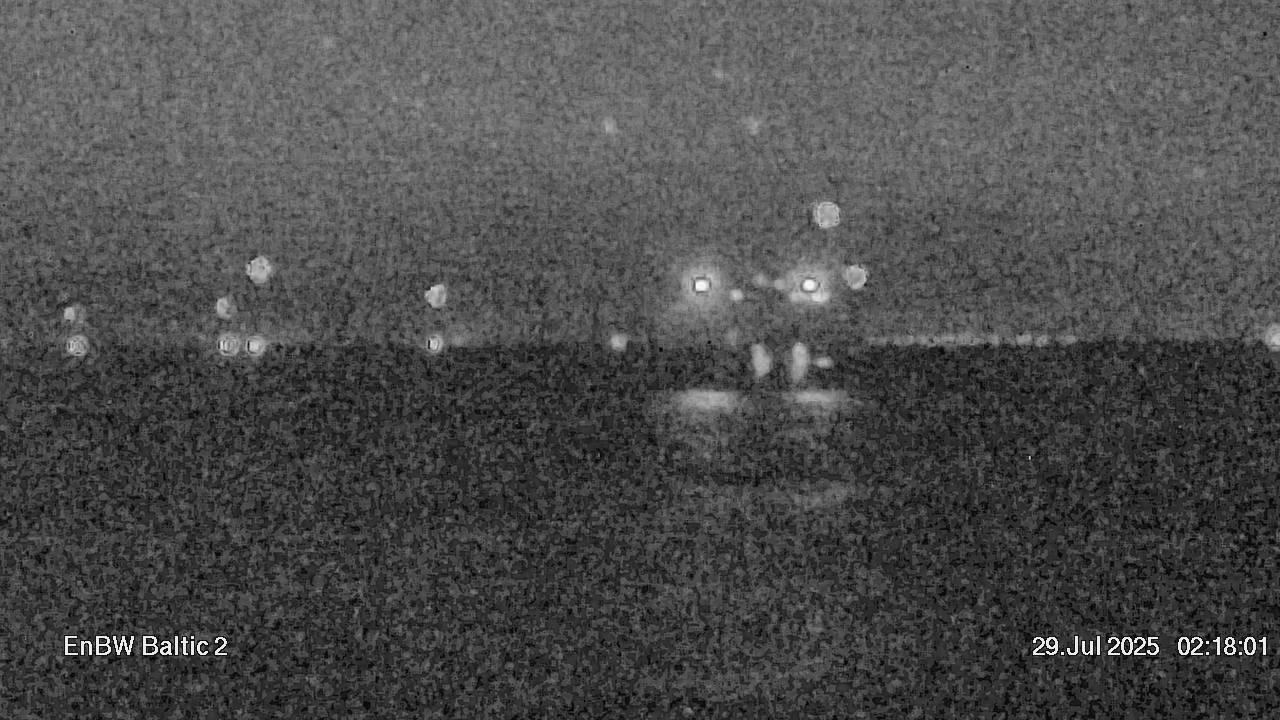
Die Fakten
Standort:
|
Ostsee, 32 km nördlich der Insel Rügen
|
Größe:
|
ca. 27 km²
|
Windenergieanlagen:
|
80 Siemens SWT-3,6-120
|
Wassertiefe:
|
23–44 m
|
Gesamtleistung:
|
288 MW
|
Jährlicher Ertrag:
|
1,2 Mrd. kWh
|
Mittlere Windgeschwindigkeit:
|
ca. 9,7 m/s
|
EnBW Baltic 2 hat deutlich größere Dimensionen als unser erster Windpark in der Ostsee, EnBW Baltic 1. Die Anforderungen an Planung und Logistik beim Bau des Windparks waren deutlich höher. EnBW Baltic 2 hat knapp ein Drittel größere Windräder als Baltic 1. Mit einem Areal von 27 Quadratkilometern ist er viermal so groß wie EnBW Baltic 1 und kann sechsmal so viel Strom erzeugen.
Die Meerestiefe variiert zwischen 23 und 44 Meter. Je nach Wassertiefe sind die Windenergieanlagen entweder auf Stahlpfählen, sogenannten Monopiles (bis etwa 35 Meter), oder Stahlfachwerkstrukturen, sogenannten Jackets (ab rund 35 Meter), montiert. Mit einem jährlichen Ertrag von rund 1,2 Milliarden Kilowattstunden kann Windpark EnBW Baltic 2 rund 340.000 Haushalte im Jahr versorgen. Damit können 900.000 Tonnen CO₂ eingespart werden.
Wie schon bei unserem ersten Offshore-Windpark Baltic 1, haben wir auch bei Baltic 2 einen Beteiligungspartner mit ins Boot genommen: Knapp die Hälfte der Anteile (49,9 %) ist in Besitz der BSOH. Die BSOH ist eine Holding, die von der genossenschaftliche Pensionskasse PGGM und der Ärzteversorgung Westphalen-Lippe gehalten wird. 50,1 % sowie Betrieb und Wartung verbleiben in Händen der EnBW. Mit unseren Beteiligungsmodellen verschaffen wir uns zusätzliche finanzielle Spielräume für weitere Wachstumsprojekte.
Unsere Filmreportage begleitete den maritimen Baustart
Die Anlagen werden verladen und treffen im Baufeld ein
Das Bautagebuch von Baltic 2
Die 80. und damit letzte Windturbine wurde gegen 14:30 Uhr auf ihrem Fundament installiert. Damit ist die Installation aller Anlagen des Windparks EnBW Baltic 2 erfolgreich über die Zielgerade gegangen.
Der Zeitpunkt der Fertigstellung rückt näher: Die Installation der Windturbinen geht voran, die 70. von insgesamt 80 steht jetzt auf ihrem Fundament. Parallel dazu werden installierte Windturbinen in Betrieb genommen.
EnBW Baltic 2 speist die erste Kilowattstunde Strom ins Netz ein. Zu diesem Zeitpunkt sind bereits 58 von 80 Windkraftanlagen installiert. Diese werden jetzt sukzessive ans Netz gehen. Wenn der gesamte Windpark steht, hat er eine Gesamtleistung von 288 Megawatt und kann für rund 340.000 Haushalte Strom erzeugen.
Das „Trenchen“ der einzelnen Strecken der internen Parkverkabelung beginnt. „Trenchen“ bezeichnet das Einspülen der Kabel in den Seeboden zwischen den einzelnen Standorten der Windkraftanlagen.
Der letzte Link der Internen Parkverkabelung für Baltic 2 ist eingezogen, die Haupt-Installation damit abgeschlossen. Jetzt werden die Kabel angeschlossen und getestet.
Nach knapp sieben Monaten ist die Hauptinstallation der Fundamente abgeschlossen. Insgesamt wurden dafür mehr als 80.000 Tonnen Stahl verbaut. Die Hälfte der 80 Windenergieanlagen ist außerdem komplett installiert. Die Errichtung einer Anlage dauert im Schnitt 18 Stunden.
Der Ersatzkabeltank für EnBW Baltic 2 mit einem Durchmesser von 12,5 Metern, befüllt mit einem knapp 3.000 Meter langen Ersatzkabel und einem Gesamtgewicht von 180 Tonnen wird vom Rostocker Hafen zur Servicestation auf dem Gelände des Kraftwerks Rostock transportiert. Das Kabel wird hier gelagert, um für den Fall, dass eine Strecke der internen Parkverkabelung beschädigt wird, schnell reagieren zu können.
Die Großbaustelle von EnBW Baltic 2 kann zum Ende des Jahres 2014 eine positive Bilanz ziehen: Die Umspannstation OSS ist installiert ebenso wie 68 Fundamente. Außerdem sind 34 Windenergieanlagen errichtet worden. Von der internen Parkverkabelung sind bereits 59 Kabelstrecken gelegt.
Die Installation der Jackets auf die bereits gerammten Jacket Piles läuft parallel weiter. Bislang sind 24 Jackets installiert. Sie bilden die Verbindung zum Turm einer Windkraftanlage auf den Jacket Piles – ein Fundamenttyp mit dreibeiniger fachwerkartiger Stahlkonstruktion. Monopiles bestehen aus einem zentralen Fundamentrohr.
Alle Monopile/Transition Piece-Verbindungen sind jetzt im Windpark von EnBW Baltic 2 installiert. Die Kabel können weiter eingezogen werden. Die Seebefeuerung (die beleuchtete Markierung der Lokation) zeigt zuverlässig die Position an.
Ein großer Meilenstein wird erreicht: Das 39. und damit letzte Transition Piece wird als Verbindung zum Turm der Windkraftanlage auf das Monopile-Fundament gesetzt. Dass das Wetter bei Offshore-Arbeiten nicht immer das beste ist, zeigt die Aufnahme vom Verladen des Transition-Piece im Hafen.
Mittlerweile sind 21 der 80 Windkraftanlagen installiert. Weitere Anlagen folgen sukzessive. Die Finalisierung des Netzanschlusses hat in nächster Zeit oberste Priorität.
Das 150 kV-Seekabel ist auf der Umspannstation eingezogen. Im sogenannten Cable-hang-off wird es befestigt. Die Armierung wird entfernt und die einzelnen elektrischen Leiter bis zur Schaltanlage gelegt.
Die Hälfte der für den Windpark notwendigen parkinternen Kabel ist gelegt. Das Installationsschiff Aura des Übertragungsnetzbetreibers 50Hertz ist im Baufeld und liegt neben der Umspannstation OSS, um mit den Einzugsarbeiten des 150 Kilovolt-Seekabels für den Netzanschluss zu beginnen. Gut zu erkennen ist der Drehteller, in dem das Kabel lagert.
Nach der Ankunft am Zielort beginnen die vorbereitenden Arbeiten, die Topside wird auf ihre endgültige Position ausgerichtet, das Jacket-Oberteil der Umspannstation abgesenkt. Um die Mittagszeit des 30. Septembers heißt es dann: Touchdown! Alle vier Beine des Jacket-Oberteils sind in das Unterteil eingefädelt und komplett abgesenkt – die OSS ist erstmalig mit der Ostsee verbunden.
Beim ersten Mal wollte das Wetter nicht mitspielen, jetzt sorgen strahlender Sonnenschein und eine ruhige See für ideale Voraussetzungen: Die Umspannstation für den Offshore-Windpark EnBW Baltic 2 tritt erneut die rund 50 Stunden lange Reise in das Baufeld an.
Beim Verlassen des Hafens in Kiel scheint noch die Sonne: Mitte September tritt die Umspannstation OSS ihre Reise in das Baufeld an. Doch am Zielort angekommen, verhindert ein Wetterumschwung die Installationsarbeiten. Der 4.400 Tonnen schwere Koloss muss den sicheren Hafen von Sassnitz anfahren.
Premiere: Die erste Windkraftanlage für EnBW Baltic 2 wird errichtet.
Das Installationsschiff Vidar wartet im Baufeld auf besseres Wetter, um die ersten Windkraftanlagen zu errichten.
Der Bau der Umspannstation in Kiel geht voran. Die Umspannstation hat bereits ein EnBW-Logo erhalten.
Ein Pile (Fundamentteil) zur Verankerung der späteren Umspannstation wird im Meeresboden verankert.
Die Taklift 4 hat das erste von 41 Jacket-Fundamenten gesetzt.
Das erste Jacket-Fundament ist von Trelleborg aus auf dem Weg ins Baufeld von EnBW Baltic 2.
Das erste Jacket-Fundament ist von Trelleborg aus auf dem Weg ins Baufeld von EnBW Baltic 2.
Das Kabellegeschiff (im Vordergrund) zieht das erste Kabel ins Fundament ein. Das Schiff „Siem Garnet“ (im Hintergrund) hat die nötige Ausrüstung gebracht.
Das Installationsschiff Vidar kommt im Hafen Sassnitz an.
Sie wird in Kürze die Windkraftanlagen errichten.
Das Transition Piece wird auf das bereits im Meeresboden verankerte Monopile gesetzt.
Der Bau der Umspannstation der EnBW in Kiel geht in großen Schritten voran.
Die Installationsplattform wird mit zwei Fundamentteilen an Bord zum Baufeld von EnBW Baltic 2 geschleppt.
Drei Fundamentteile für den Offshore-Windpark EnBW Baltic 2 stehen im Hafen von Rostock.
Ein Fundamentteil wird mit einem Kran auf die Installationsplattform „Goliath“ gehoben.
Die Umspannstation hat die sechste und letzte Ebene erhalten und ist jetzt auch von der Kieler Woche aus zu sehen.
23 km Mittelspannungskabel wurden an Board des Kabellegeschiffes geladen.
Das erste Jacket (Fundamentteil einer Windkraftanlage) wird aus dem Dach der Werkhalle in Lindoe/Dänemark gehoben. Es ist ca. 55 m hoch und hat ein Gewicht von ca. 580 Tonnen.
Die Installationsplattform Goliath ist nach ihrem Einsatz in der Ostsee gestern kurz vor Mitternacht wieder im Hafen Rostock angekommen. In den vergangenen Monaten hat sie Stahlröhren (Jacketpiles) im Meeresboden verankert. In den nächsten Wochen wird sie umgerüstet, um ab dem Frühsommer weitere Fundamentteile auf der hohen See zu installieren.Das erste Jacket (Fundamentteil einer Windkraftanlage) wird aus dem Dach der Werkhalle in Lindoe/Dänemark gehoben. Es ist ca. 55 m hoch und hat ein Gewicht von ca. 580 Tonnen.
Die erste fertige Turbine von EnBW Baltic 2 hat in Brande in Dänemark ihr Logo erhalten.
Die Arbeiter auf der „Goliath” haben die letzten Jacketpfähle in den Meeresboden gerammt. Ein wichtiger Teil der Fundamentarbeiten ist damit abgeschlossen.
Ein weiterer Jacketpfahl wird aufgerichtet
Nachts beginnen am 41. Standort die Arbeiten, um die letzten Jacketpfähle im Meeresboden zu verankern.
Die Transition Pieces vor ihrem Transport von Bremen nach Lindö. Dort werden sie mit den fertigen Jackets verschweißt.
Fertige Fundamentteile (Transition Pieces für die Jackets) beim Verladen auf eine Transportplattform.
Fertig zusammengebaute Gitternetzstrukturen.
Die Gitternetzstrukturen der sogenannten Jackets (Fundamentteile) werden zusammengebaut.
Fertig produzierte Kabel für die interne Parkverkabelung.
Produktion der Transition Pieces für die Monopiles in Rostock.
Die Ebene 5 des Jacket-Oberteils wird in die Umspannstation gehoben.
EnBW hat heute das letzte der 39 Monopiles gesetzt.
Die Fundamentteile (Monopiles und Jacketpiles) an der Kaikante in Rostock. Monopiles werden gerade auf das Transportschiff geladen.
Üben für den Ernstfall: Der Notarzt wird mit der „verletzten Person“ in der Krankentrage von der „Goliath“ zum Rettungshelikopter hochgezogen.
Rettungsübung: Rettungshelikopter fliegt zur Installationsplattform „Goliath“. Links von der Plattform bringt ein Schlepper den Rettungsassistenten zur „Goliath“.
Dabei ist der „Große Blasenschleier“ zum Schutz von Meeressäugern im Einsatz.
14. Oktober 2013
Das Monopile wird aufgerichtet und ins Wasser gelassen und…
… im Meeresboden verankert.
Der Deckel des Monopiles wird abgenommen.
Der Hammer wird mit dem Kran in die richtige Position gebracht.
Ein Schlepper hat das selbst schwimmende Monopile zur Svanen gebracht.
Der hydraulische Hammer zum Verankern der Fundamente, der sogenannten Monopiles.
Ein Zimmer für Offshore-Mitarbeiter an Bord der Installationsplattform Svanen.
14. Oktober 2013
Schlafplatz an Bord der Svanen.
Die Installationsplattformen Goliath (links) und Svanen sind im Baufeld bei der Arbeit. Insgesamt haben sie 18 Jacketpiles und 7 Monopiles im Meeresboden verankert.
Die beiden Trafos für die Umspannstation werden in Kiel angeliefert und in der nächsten Zeit in die Umspannstation eingebaut.
Dieser Generator wurde in Estland gefertigt und nach Dänemark transportiert. Dort wird er in die Gondel einer späteren Windkraftanlage eingebaut.
Das Monopile wird aufgerichtet und mit einem hydraulischen Hammer rund 35 m in den Boden gebracht.
Im Baufeld nimmt die Installationsplattform Svanen das Monopile an den Haken. Die Deckel werden abgenommen.
Am Haken eines Schleppers wird es in rund 15 Stunden ins Baufeld gebracht.
Der zweite Fundamenttyp, ein sogenanntes Monopile wurde mit zwei Deckeln verschlossen und schwimmt damit selbst.
Der Hammer, der die Jacket-Pfähle in den Meeresboden rammt, wird ins Meer abgesenkt und auf einen Jacket-Pfahl gesetzt.
Ein Jacket-Pfahl wird in das Meer abgelassen. Eine Schablone dient unter Wasser dazu, die Pfähle an den für sie vorgesehenen Standort niederzulassen.
Ein Jacket-Pfahl wird aufgerichtet.
Es werden Vorbereitungen zur Aufrichtung der Jacket-Pfähle getroffen.
Die Installationsplattform „Goliath“ nimmt die Jacket-Pfähle mit einem Kran entgegen.
Die Installationsplattform „Goliath“ hat den Rostocker Hafen verlassen und die rund zwölfstündige Fahrt in das Baufeld von EnBW Baltic 2 aufgenommen.
Zwischen den Beinen der „Goliath“ hat das Template die korrekte Position erreicht, dort ist es mit Seilzügen befestigt.
Die Montage des sogenannten Templates unter die „Goliath“ wird vorbereitet. Es dient später als Schablone, um die Jacket-Pfähle auf dem Meeresboden maßgenau zu positionieren.
Die Jackets werden verladen. Sie haben eine Länge von rund 48 – 64 Metern, einen Durchmesser von 3 Metern und ein Gewicht von rund 150 – 190 Tonnen.
In Drammen, Norwegen, wird mit der Produktion der Kabel begonnen.
Das Transportschiff für die Jacket-Pfähle, die „Abis Dundee“, trifft im Hafen von Rostock ein. Sie wird immer sechs Jacket-Pfähle ins Baufeld transportieren
Die Goliath kommt in Rostock an und wartet darauf, die JKT-Piles laden zu können.
Der Rammhammer wird auf die Installationsplattform „Goliath“ geladen.
Die Baufeldüberwachung (Work Vessel Coordination) hat im Baubüro in Sassnitz ihre Arbeit aufgenommen und ist bereit für den baldigen Baustart.
Fertigungsstart für die Jackets in Lindoe, Dänemark.
Die EnBW hat im Vorfeld Fundamente (Testpfähle) im Baufeld gerammt, um ihre Tragfähigkeit zu bestätigen. Diese Pfähle werden jetzt abgeschnitten und entfernt.
Alle 123 Jacket-Pfähle sind fertiggestellt. Bald werden sie im Baufeld im Meeresboden verankert. Jeweils drei Jacket-Pfähle dienen zur Verankerung für ein Jacket-Fundament. Die 41 Jackets werden in einem zweiten Schritt installiert.
In der vergangenen Woche wurden für die internen Parkverkabelung die Kabelschutzsysteme und Bellmouth fertiggestellt. Die Bellmouth stellt die Kabeleinführung in das Fundament dar.
EnBW nimmt die erste produzierte Kabellänge bei Draka in Nässjö (Schweden) ab. Die Kollegen haben vorher die Qualität überprüft.
Eine der vier Großsektionen der Umspannstation wird aus der Fertigungshalle mit einem Brückenkran in das Trockendock gebracht. Diese Großsektion wurde vorher bereits innen beschichtet.
Von dem Spezialschiff „Aura" aus wird nun der erste Seekabelabschnitt für die Anbindung von EnBW Baltic 2 in den Ostseegrund eingespült. Insgesamt sind in den kommenden Monaten sechzig Kilometer Seekabel zu legen.
Der erste Seekabelabschnitt wird durch den Transportnetz-Betreiber „50Hertz“ in die Offshore-Plattform des Windparks EnBW Baltic 1 eingezogen. Über diese Plattform wird künftig auch der EnBW Baltic 2-Strom an Land gebracht.
Anfang April ist bereits ca. ein Viertel des Gesamtvolumens der Jacket-Pfähle produziert. Die Pfähle warten auf dem Lagerplatz auf die letzten Arbeiten und auf das Verladen aufs Schiff.
Für die Verlegung der Seekabel kommt ein Räumpflug zum Einsatz, der den Meeresboden von Hindernissen (Steine) befreit und 1,5 Meter tiefe Furchen in den Boden gräbt
Mit dem Brennstart beginnt bei der Firma EEW-SPC in Rostock die Herstellung der Pfähle, die später die Jacket-Fundamente im Meeresboden verankern. Insgesamt werden 123 Pfähle mit einem Durchmesser von 3000 mm benötigt.
Technik von Baltic 2
80 Windkraftanlagen und eine Umspannstation zu errichten und die gesamte Fläche von 27 km² mit rund 85 km Tiefseekabel zu vernetzen, erfordert eine präzise Planung. Alle einzelnen Prozesse müssen genau aufeinander abgestimmt werden: Erst wenn die Fundamente errichtet sind, können die Kabel innerhalb des Parks verlegt werden. Dann werden die Windkraftanlagen gebaut. Die Umspannstation muss rechtzeitig vor der Parkverkabelung und der ersten Turbine errichtet sein.
Unsere Bauleiter und Logistiker erwarten anspruchsvolle Aufgaben: die Abschätzung der Arbeitsgeschwindigkeiten, die Berechnung der Transportwege – und die Abstimmung auf die Wetterlage.
Allein ein Schiff für die Windkraftanlagen, bis zu zwei Schiffe für die Gründungsstrukturen und bis zu drei Schiffe für die Verkabelung kommen aus unterschiedlichen Häfen und zu verschiedenen Zeiten ins Baufeld, das zusätzlich von einem Verkehrssicherungsschiff gesichert wird.
Das Meer ist ein eigenwilliger Projektpartner: Es darf nicht zu kalt sein, sonst härtet der Spezialzement nicht aus, mit dem die Bauteile der Fundamente verbunden werden.
Die Umspannplattform braucht ruhige See, um ans Ziel zu gelangen und sich eigenständig zu errichten. Die Windkraftanlagen können nur bis zur Windstärke 4-5 installiert werden.
Für jede Bauphase müssen nicht nur sämtliche Komponenten ins 32 km von der deutschen Küste entfernte Baufeld transportiert und installiert werden – auch die Crews werden regelmäßig ausgewechselt.
Die Crewtransferschiffe fahren von unserem Basishafen Sassnitz Mukran zwar nur rund 2 Stunden, doch braucht eine schwere Installationsplattform bis zu ca. 12 Stunden, um ins Baufeld zu gelangen. Da heißt es, an alles denken – denn jede Verzögerung kann einen sechsstelligen Eurobetrag am Tag kosten.
In der Ostsee findet sich die gleiche weiße Kreide wie bei den berühmten Kreidefelsen von Rügen. Darüber lagert der so genannte Geschiebemergel, eine Sedimentschicht, die sich beim Abschmelzen der eiszeitlichen Gletscher gebildet hat. Für eine stabile Verankerung reichen die Fundamente von 36 m bis 55 m tief in den Erdboden hinein.
Jedes Fundament muss den unterschiedlichen Meerestiefen von 23 m bis 44 m einzeln angepasst werden. Je nach Wassertiefe werden bis 35 m Monopiles eingesetzt. Ab 35 m kommen dreibeinige Jackets zum Einsatz.
Die Monopiles und die Gründungspfähle der Jackets werden mit einer Ramme von einem Spezialschiff aus in den Meeresboden gebracht. Über die Monopiles werden anschließend wie eine Manschette die so genannten Transitionpieces gestülpt, die das Fundament mit dem Turm verbinden, und mit einem Spezialzement fest verbunden.
Für die dreibeinigen Jackets wird die Position der Gründungspfähle durch große Schablonen, so genannte Templates, am Meeresboden genau bestimmt.
Dann erst werden in einem zweiten Arbeitsgang die Jackets auf die Pfähle gesetzt und mit einem Spezialzement fest verbunden. Diese Installation eines Fundaments kann je nach Wetterbedingungen bis zu fünf Tage dauern.
Die Komponenten werden an verschiedenen Standorten in Dänemark hergestellt und in unseren Basishafen Sassnitz Mukran geliefert. Hier werden die Stahltürme, die Gondeln und die Rotorblätter auf einer Fläche von 80.000 qm gelagert und 2-3 Monate vor Installationsbeginn vormontiert.
Auf einer schwimmenden Montageplattform können Komponenten für mehrere Anlagen ins Baufeld geschleppt werden. Um die gewaltigen Gewichte zu heben, steht die Plattform auf Beinen fest auf dem Meeresgrund und stemmt sich rund 10-15 m über den Wasserspiegel empor. Von dieser Plattform aus wird jede Anlage in rund 36 Stunden installiert.
Die 256 t schweren und rund 66 m hohen Stahltürme werden mit einem Kran auf die Fundamente aufgesetzt und verschraubt. Die rund 150 t schwere Gondel wird mit dem Generator und dem Getriebe montiert. Zuletzt werden die einzelnen Rotorblätter montiert.
Die 40 x 40 Meter breite und 14 Meter hohe und 4.400 Tonnen schwere Umspannplattform schwimmt von alleine. Das spart nicht nur Transportkosten – auch die Installation der Plattform ist weniger aufwändig: Den Oberteil ihres Fundamentes bringt sie nach innen eingefahren mit und kann sich daher selbst auf den vorinstallierten Unterteil gründen.
Zuerst ziehen Schlepper die Umspannplattform von der Werft ins Baufeld. An Ort und Stelle angekommen, fährt sie ihre Jacket-Gründungsstruktur nach unten aus und stemmt sich rund 1 m über den Meeresspiegel empor. Lediglich die Unterkonstruktion, auf der die Jacketstruktur aufsitzt, muss vorher über Gründungspfähle im Meeresboden verankert werden.
In der Umspannstation fließt der Strom aus den 80 Windkraftanlagen zusammen und wird von einer Spannung von 33 kV auf 150 kV transformiert. Eine niedrige Spannung erfordert für den Stromtransport zur Vermeidung von Übertragungsverlusten ein sehr dickes Kabel.
Um die kilometerlange Unterwasserverlegung eines solchen Kabels zu vermeiden, wird der Strom möglichst dicht an der Erzeugungsquelle umgewandelt: Die Umspannplattform wird daher im Windpark auf hoher See und nicht an Land installiert.
Das interne Stromnetz des Windparks ist rund 85 km lang. Die Kabel werden aus Norwegen direkt ins Baufeld transportiert.
Nicht nur der Strom wird über die 11,9 bzw. 14 cm dicken Tiefseekabel transportiert, auch die Informationen und Daten zwischen den Anlagen und der Leitwarte in Barhöft werden über hochsensible Lichtwellenleiter ausgetauscht, die in die Kabel eingebunden sind.
Das so genannte Exportkabel transportiert den Strom von der Umspannstation über EnBW Baltic 1 zum nächsten Umspannwerk an Land. Hier wird die Spannung im Umspannwerk Bentwisch erneut von 150 kV auf 380 kV hoch transformiert und von der 50Hertz Transmission GmbH in das deutsche Verbundnetz eingespeist.
Partner - Unsere Lieferanten und Dienstleister
An Planung, Logistik und Bau unseres Windparks sind viele führende internationale Unternehmen aus der Windkraft- und Offshore-Branche, aber auch regionale Spezialisten beteiligt.
Gründungen
(Design, Fertigung, Transport und Installation): |
Joint Venture HGN (Hochtief Solutions, GeoSea, Nordsee Naßbagger) Hamburg, Deutschland
|
Interne Parkverkabelung:
|
Transport und Legung: Siem Offshore Contractors GmbH, Leer, Deutschland
Kabelfertigung: DRAKA, Drammen, Norwegen |
Umspannplattform
(Design, Fertigung, Transport und Installation): |
Joint Venture Alstom Weserwind, Bremen, Deutschland
|
Windkraftanlagen
(Design, Fertigung und Installation): |
Fertigung: Siemens Windpower, Brande, Dänemark
Transport und Errichtung: Joint Venture HGN (Hochtief Construction, GeoSea, Nordsee Naßbagger), Hamburg, Deutschland |
Bereitstellung der nötigen Hafeninfrastruktur:
|
Fährhafen Sassnitz/Mukran
|
Lieferung der Kabelschutzsysteme:
|
Tekmar Energy Ltd., Newton Aycliffe, UK
|